Job management
- Optimisation of production according to the real production situation (condition of individual machines, order priorities, stock of material, etc.).
- Simplified order planning
- Accurate information about machine condition
- Detailed information about production orders
The Job management function displays an overview of work orders and operations directly on the control panel of the machine tool, which is connected to the company's ERP system (including a desktop application for the foremen of the production hall). Enables optimisation of production using logical algorithms that evaluate the priority of individual orders according to the completion date, machine condition or material stock in the warehouse.
Various supporting documents can be included in the application, such as a description of the operation, photos, tables (clamping instructions, etc.) and also NC programs.
Immediate overview of currently executed production orders on a given machine, or on all machines in the production hall. As a result, we need to make production planning more efficient based on information about the utilisation of individual machines, specified dates, availability of materials in stock and possibly other available information.
Remote diagnostics
- Remote screen display of the control system of the connected machine including its remote control
- Remote control of the machine system, including control of its internal parameters
- Remote diagnosis of drives, measurement and indication of machine inputs/outputs
- Quick remote verification of machine errors/defects – interactive transmission of machine status data
- In the event of an electronic problem, there is an immediate remote solution
- Data transfer to the customer's control system for the purpose of support in the technological use of the machine (transfer of NC programs, tool tables and zero points) and in the correction of its properties (transfer of PLC programs and machine parameters)
The technical means of our service is the possibility of remote connection using an Internet connection to the machine at the customer's place (we have the relevant software in the company and after enabling the service on the customer's side, we are able to connect to the machine remotely).
Remote diagnostics is offered for all machines manufactured by TOS VARNSDORF a.s. that are equipped with a HEIDENHAIN TNC 640 or SINUMERIK 840D Sl control system.
Technically, the system is designed in such a way that the customer's machine is equipped with a communication unit (combination of modem, router and switch) which, upon the request of the machine operator, sends a request via the Internet to connect with the service operator on the manufacturer's side (the system is equipped with security certificates and keys for creating secure connection).
It is a great advantage to have a remote overview of the function and condition of the machine practically from all over the world. Our remote diagnostics system makes this possible.
TOScontrol
TOScontrol is a set of applications and functions for advanced machine management. For easy and intuitive operation, the system contains a default screen with icons of individual applications (similar to the operating systems of mobile devices).
The applications are clearly displayed on the machine control panel, and the operator can seamlessly switch between them. The solution also includes the management of user accounts. TOScontrol is part of the standard equipment of all machines.
- Online exchange of data in the ERP system
- Special applications to extend functionality
- User friendly interface
- The standard equipment is a DNC module that enables communication between the machine and a PC
- Clearly arranged system for controlling the additional functions of the machine
- Easy operation and information always on the screen of the control system
- Comprehensive overview of machine activity and conditions
- Security ensured by user authorisation
- Functions for connecting the machine to ERP via the UPC-UA interface
We named the control system superstructure “TOScontrol”. It is a suite of applications and functions for advanced machine management.
For easy and intuitive operation, the system contains a default screen with icons of individual applications (similar to the operating systems of mobile devices).
The applications are clearly displayed on the machine control panel, and the operator can seamlessly switch between them. The solution also includes the management of user accounts.
Industry 4.0 offers virtually unlimited possibilities in the field of connecting machines to production systems, their integration, including a high degree of automation for complex control and monitoring of the quality of the production process.
Our objective is to offer a superstructure of the classic machine control system that offers many special functions.
Standard machine equipment
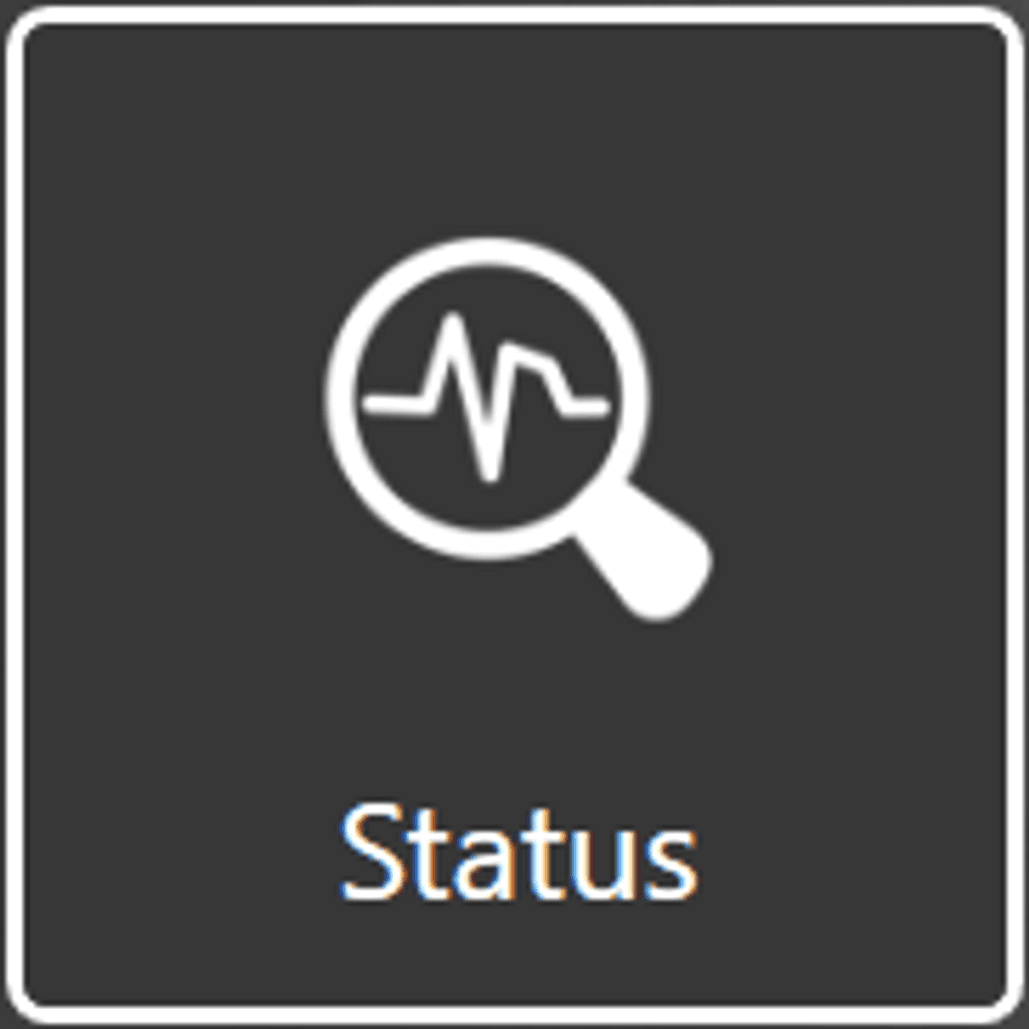 |
STATUS SCREEN Clearly displays basic information about the machine (coordinates, program, alarms, logged in user, etc.).
|
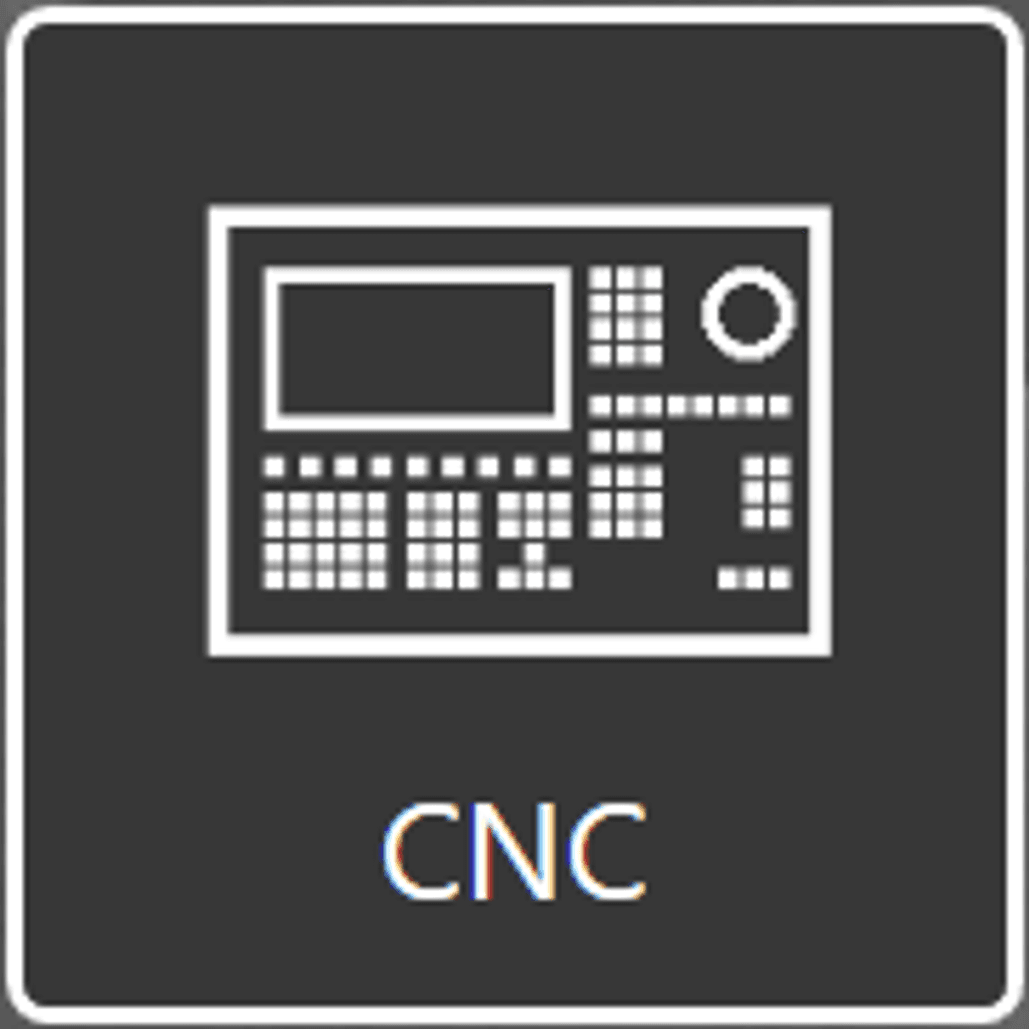 |
CNC CONTROL SYSTEM Displays the standard control system screen supplemented by a sidebar with a button for returning to the TOScontrol home page.
|
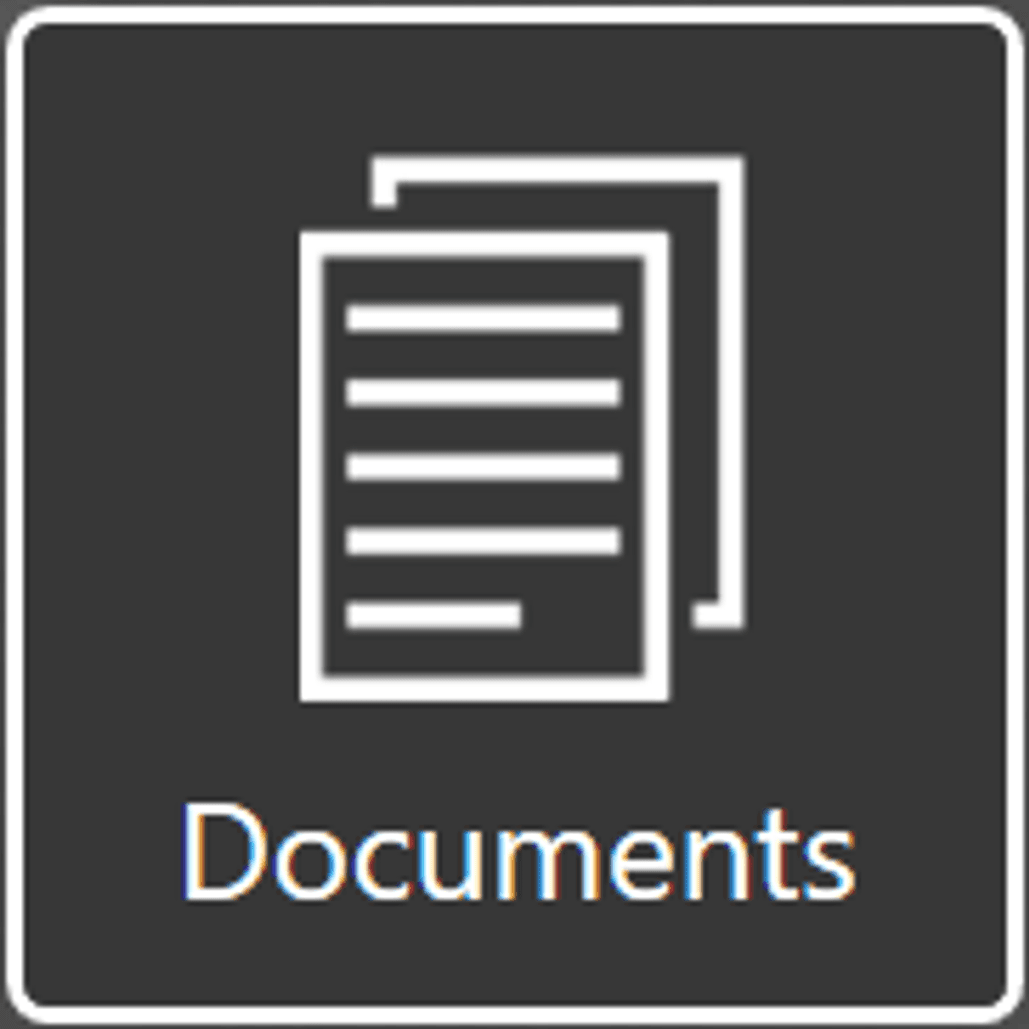 |
DOCUMENTATION This is an application enabling the reading and management of PDF documents (e.g. operating instructions, repair manual, etc.), including the possibility of user rights creation and creation of tabs and notes in documents.
|
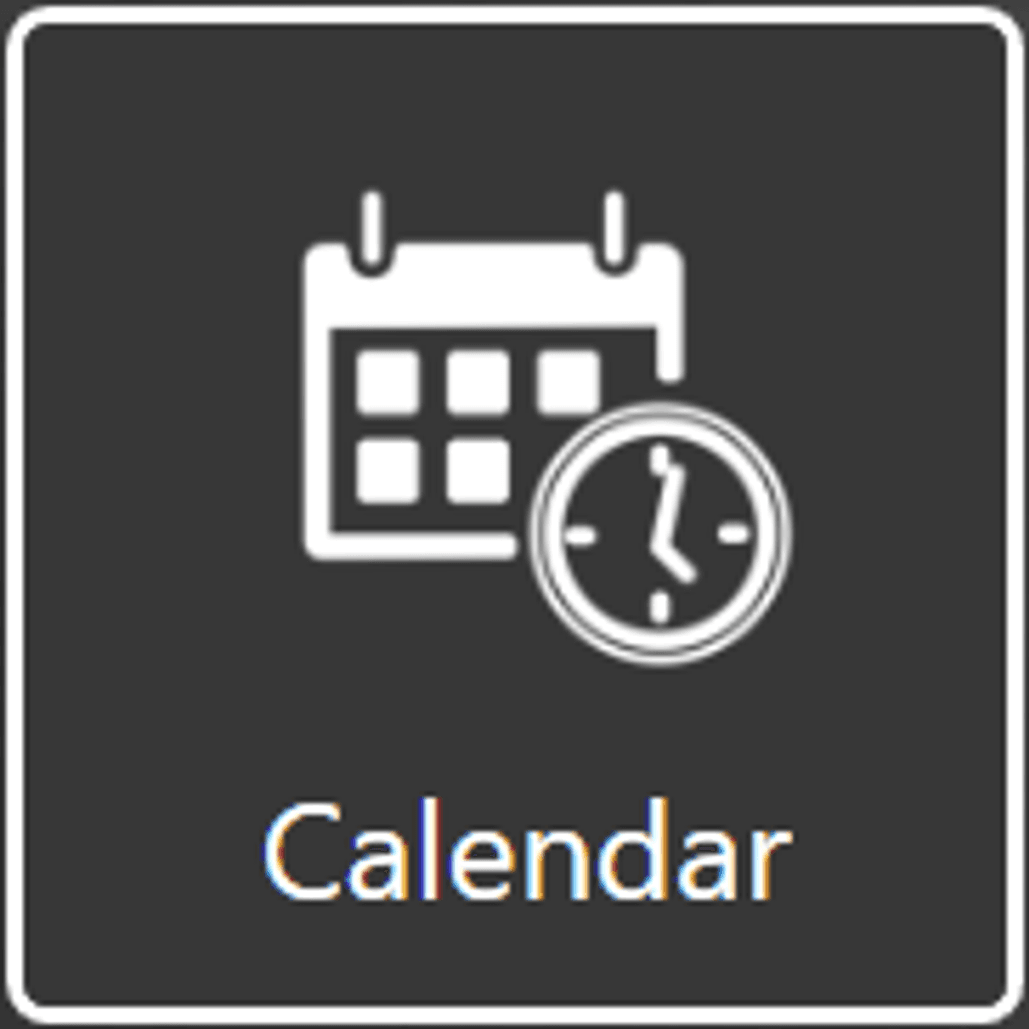 |
CALENDAR Standard calendar view – day, week, month. Event / service activity – add, change, delete, remind. All data stored in the local database. |
Option applications
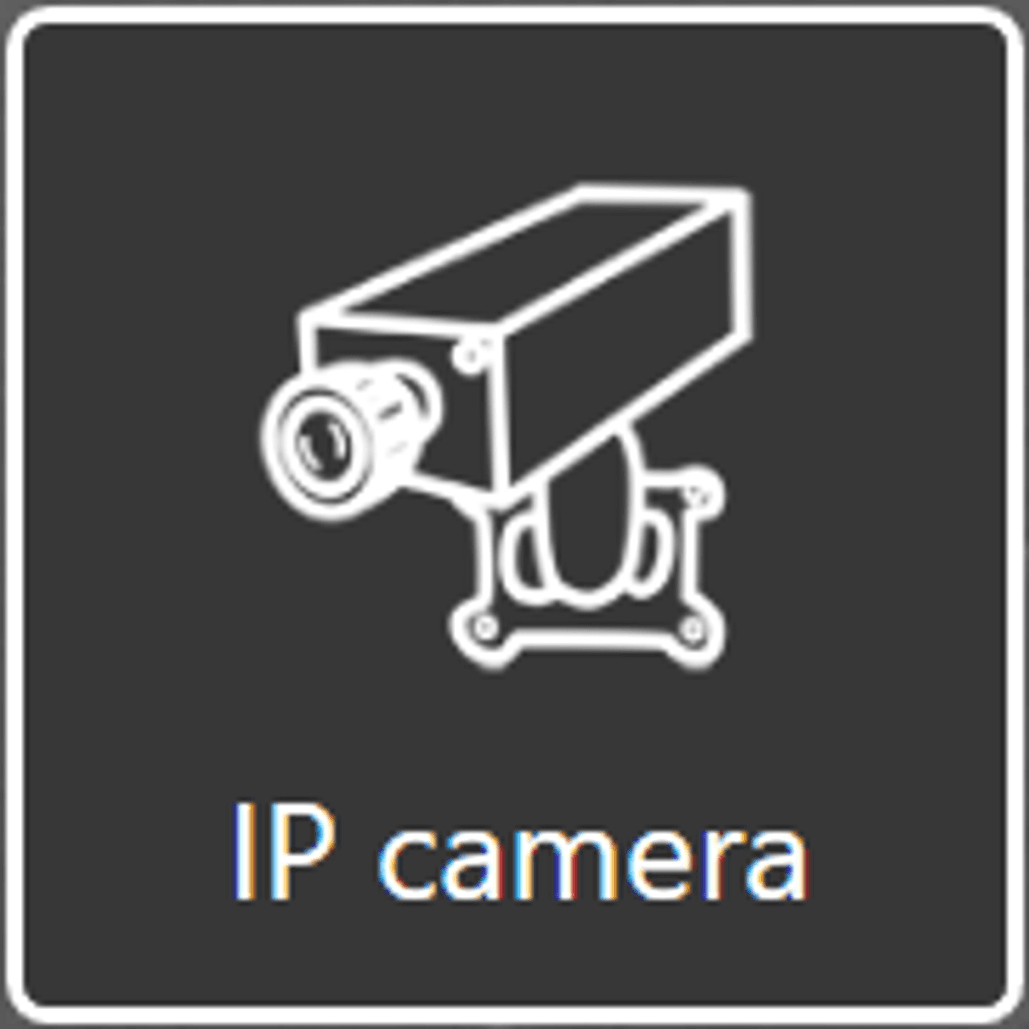 |
IP CAMERA The application enables control of one or more motorised cameras located on any part of the machine. Data from the camera can also be used to facilitate machine operation.
|
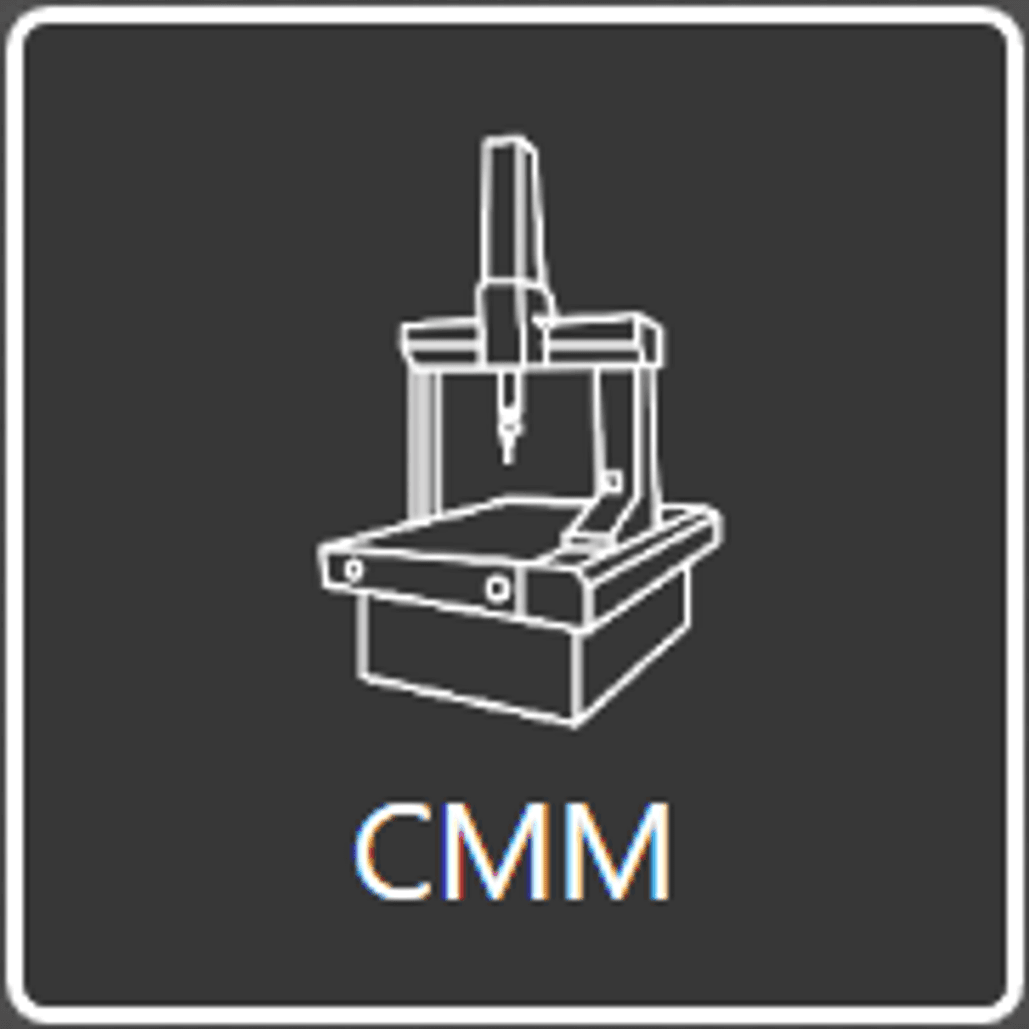 |
INSPECTION AND COMPENSATION This is metrological software integrated into the control system, which together with the touch probe allows the work-piece to be measured accurately and directly on the machine making it possible to perform the automatic compensation of errors and program debugging.
|
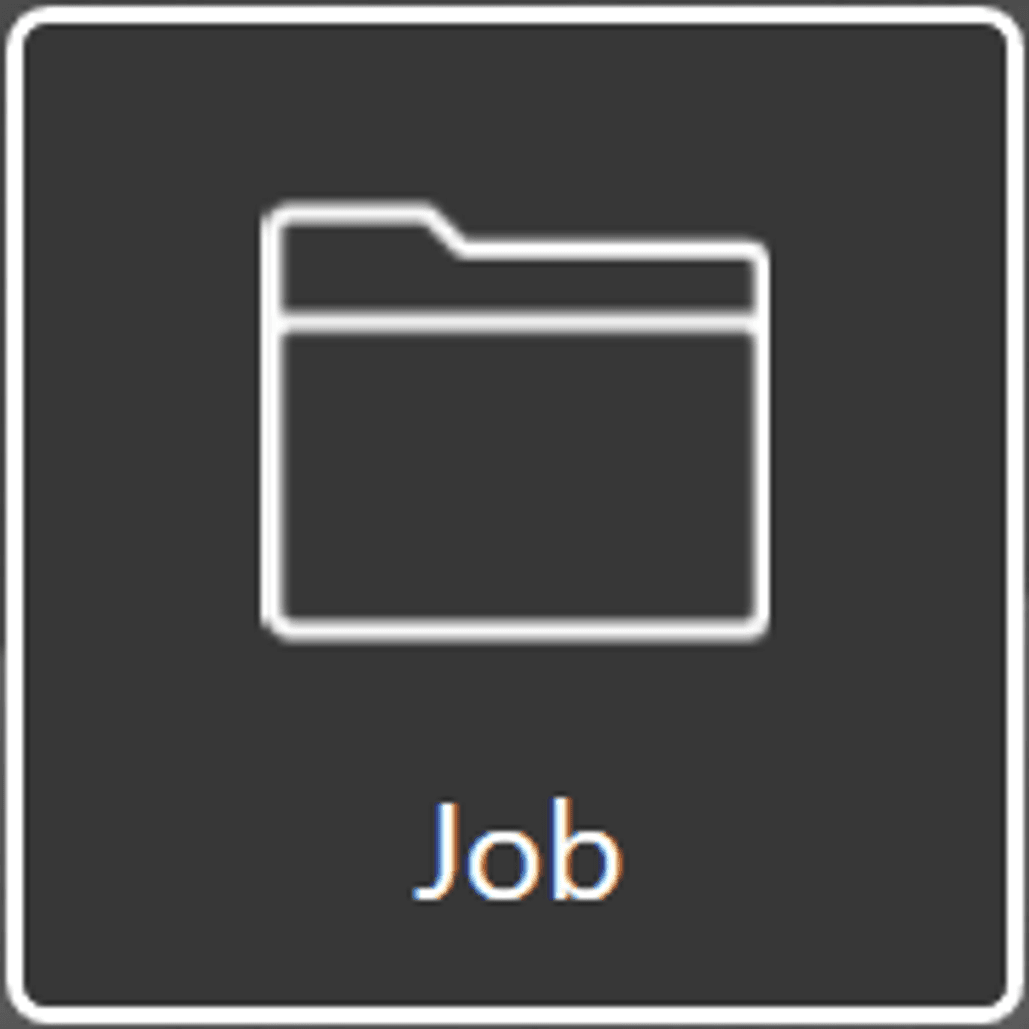 |
WORK ADMINISTRATOR Used to display the work order view and the overview of operations directly on the machine tool control panel, which is linked to the ERP system. It is also possible to add other documents into the application, e.g., operation description, photographs, tables of NC programs.
|
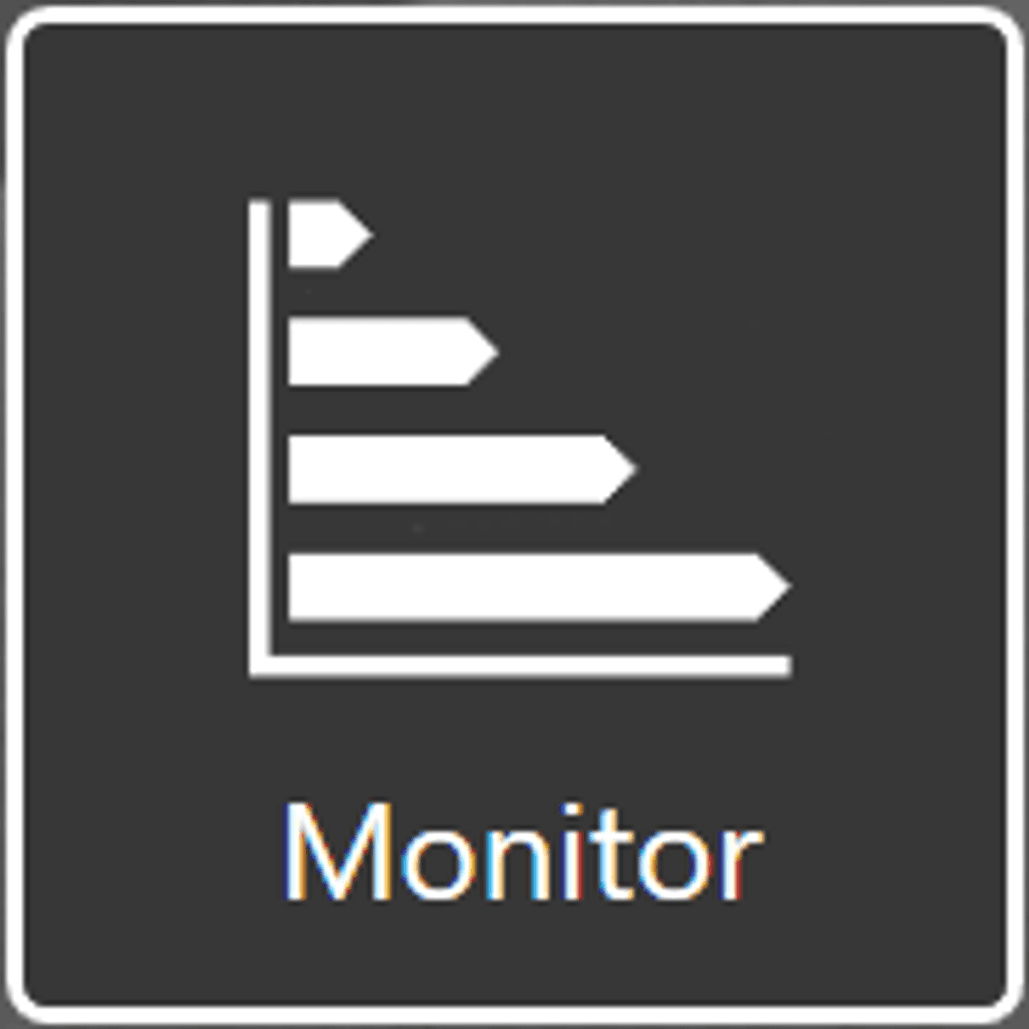 |
MACHINE MONITOR An integrated system for monitoring the history of machine tool use. This system displays the time axis of basic machine states, e.g., ready, production, production slowdown, error, off, etc. |
Easy head calibration
- Time saving – easy and quick adjustment of head kinematics
- Increasing the accuracy of head positioning (high adjustment accuracy)
- Unlimited repeatability of use
This function automatically measures the head rotational axes using the touch probe cycle. To measure the rotary axes, a calibration ball is fixed anywhere on the machine table, which is detected using a touch probe. Based on the measured values, the system detects spatial errors resulting from axis tilting. The cycle calculates an optimised kinematic description of the machine, in which these errors are minimised, and stores it in memory as machine kinematics. Of course, a file with a measurement report is also available. In addition to the measured values, this file also contains the optimised variance (a measure for static rotation accuracy) as well as the actual correction data. In order to use the function optimally, you need a particularly stiff calibration ball. This eliminates deformations caused by force acting on the probe tip.
Manual calibration of the milling head is a lengthy process without knowledge of the appropriate functions or procedures.
Work volume monitoring
- A detailed view of the cut position without the need to enter – increased operator safety
- A complete overview of the machining process on one screen
- An excellent overview of the automated machine activities performed
- Remote diagnostics improvement
The system allows the image from one or more cameras to be displayed on the machine control panel screen. It is also possible to control (tilting and zoom) installed cameras located on any part of the machine, including the machine work volume.
It is not possible for one person to simultaneously monitor the workpiece and other areas/functions of the machine.
The aim of the solution is to enable monitoring of multiple activities simultaneously (on one screen).
Headstock balancing
- Lower feed forces are needed to move the axis (especially when moving up)
- Minimum energy consumption during position bond
- Extending the service life of the mechanical parts of the guide and the drive of the vertical axis
On TOS VARNSDORF machines the weight of the headstock is balanced (depending on the machine type) by means of counterweights inside the column or by means of a hydromechanical system.
With these systems we reduce the sliding forces necessary to control the axis and minimise the consumption of electrical energy when stopping the axis in position. Thanks to a balancing system without introducing additional forces into the frame and the guide, we significantly reduce the wear of the ball screws of the Y axis.
As the headstock moves, the ball screw motors on the Y-axis must constantly overcome gravity. Our goal is to minimise this effect in order to increase the efficiency and precision of the vertical axis motion control.
Integrated metrological system
- Significant time savings (no need to move the workpiece to the measuring machine and back)
- The machine tool is directly controlled using the metrology software – ease of use
- Elimination of internal machine errors
- Correction of errors/inaccuracies on the workpiece without changing the NC program
Integration of a metrology system (3D coordinate measuring machine) with a touch probe into the machine tool, thanks to which it is possible to precisely measure workpieces directly on the machine. Internal machine errors are eliminated by using an independent measuring device – an external "Leica" laser measuring system.
During measurement, the machine tool is operated in the same way as a 3D coordinate measuring machine. The system also enables automatic transfer of measured errors to the control system of the machine tool as a correction added to the CNC program (the machine can eliminate machining errors without the need to change the program).
Inter-operational and final measurements of workpieces with sizes of approx. 1 m3 or larger consume an unproportional amount of time in transport and handling to the measuring centre and back to the machine for repair.
The aim is to minimise these losses in production.